What is Reflow Soldering?
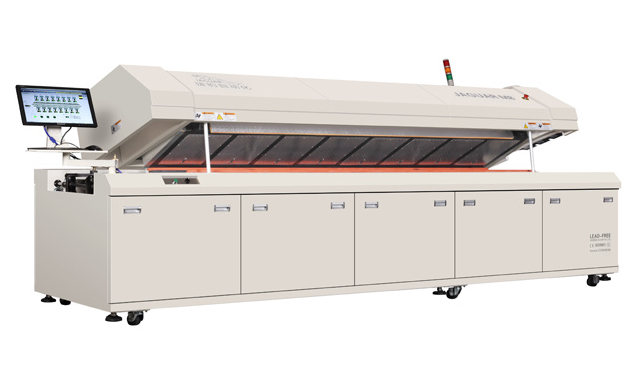
Reflow soldering is a soldering process that is used to solder components on a Printed Circuit Board. A mixture of solder paste and flux is deposited on the PCB where the component leads need to be connected to the copper traces. The paste is sticky, so the components stick to the board. The PCB is then passed through a reflow oven which is maintained at a particular temperature that results in the formation of solder joints.
The reflow soldering process consists of four stages - preheat, soak, reflow and cooling. All four stages have a carefully controlled temperature gradient measured in Celcius per second which is stipulated in IPC-7530 to be around 3 Degrees Celcius/Second.
The PCBs undergo linear heating in the preheat phase where the goal is to get the PCBs to soak temperature without any cracking or deforming of the ICs, and the PCB. This step is also important to allow any volatile liquid trapped in the solder or the PCB to evaporate.
The PCBs then stay at the soak temperature for 60 to 120 seconds till all parts of the PCB are at the same temperature. The PCB is now primed and the reflow process can begin. During the reflow process the PCB is taken to a temperature approximately 5 degrees Celcius lower than the lowest temperature failure value of a component placed onto it, but 20-40 degrees Celcius higher than the temperature required to melt the solder and allow “wetting”, as stipulated in IPC-7530, to take place. The PCB then enters the cooling phase which occurs at 4 degrees Celcius per second.
It is important to ensure that the temperature gradient is not very steep. As if the temperature change happens too quickly, the components on the PCB develop problems, such as, cold solder joints, charred boards, tombstoning and uneven wetting. To avoid these problems the most common soaking time of 30 seconds to 2.5 minutes exist.
Types of Reflow Soldering
There are many different types of reflow soldering. A few of them have been listed below.
Infrared Reflow: In this method, the PCBA is passed under an infrared lamp. The distance between the lamp and the PCBA is 5cm/2in. The heat from the emitted radiation is used to melt the solder paste and subsequently used to form solder joint post solidification.
Infrared is the electromagnetic radiation located between microwave and visible light. 0.72 to 1.5 u is near-IR, 1.5 to 5.6 u is middle-IR and 5.6 to 1000 u is far-IR. The type of emitter used determines the wavelength of the IR used for reflow. Using IR for reflow allows greater control over the amount of penetrating energy exerted, which is very much required for an even temperature rise. Far-IR avoids the shadowing effect and is not sensitive towards color. Using IR enhances heat flow as it also heats the ambient air inside the oven.
Vapour Phase Reflow: In this method, the reflow chamber is filled with an inert hydrocarbon vapor. The hydrocarbon is present in the chamber in liquid phase, but after heating it converts into vapor phase and this hot vapour at 250 degree Celsius is used to heat the solder paste, which on solidification forms solder joints. The equilibrium and maximum allowed temperature inside the oven is a function of the boiling point of the primary hydrocarbon used for the process. This means that the process is independent of the location and the configuration of the components on the PCB. No tombstoning or shadowing effect will be observed as long as sufficient soak time is allowed. This type is useful for a low volume and high mix type of PCB. The amount of flux that has to be used is moderate as this reflow occurs in an oxygen free environment, as all of it is expelled by the inert fluorocarbon vapor.
Forced Convection Reflow: This method is similar to vapor phase reflow, which one major difference is that instead of a hydrocarbon as the vapor used to heat the solder paste, this method used hot air being blown perpendicular to the surface of the PCB to melt the solder paste.
This method utilizes forced convection in the upper and lower part of the chamber. This method uses a perforated panel type heater with a plenum behind it. The heated air is sent over the PCB to melt the solder, it is then suctioned off by the ducts between the perforated panels. Higher end ovens use a perpendicular to the surface of the PCB gas flow technique t provide uniform heating of the PCB.
The disadvantage of this system is that it uses a large amount of gas to heat the PCB. Making the air oxygen-free is also a cost additive challenge. This causes solder balling and lesser wetting problems compared to the IR-reflow method.
In-line Conduction Reflow: This system employs a heated belt which to heat the PCB from the underside. The belt is made of fiberglass impregnated with PTFE. All Teflon belts have carbon added to them to make them electrically conductive. This allows the belt to be externally grounded using a wiper brush. This system uses an IR heating element to heat the PCB from the top while using the belt to heat the PCB from the underside.
Hot bar reflow: This method is similar to InfraRed reflow, with the primary difference being that instead of using lights that emanate infrared radiation to heat the surface of the PCB. This method employs a more old-fashioned resistance heating element. Therefore this is a type of resistance soldering device. The electrode is molybdenum. The components are placed onto a printed solder paste or solder dipped, in order to aid solder flow over the top surface of the lead. Impulse heating is used to heat the top-side of the lead.
Laser reflow: This system uses light of a particular wavelength emitted from a laser or light emitted from a Nd:YAG laser. This is the best process to attach heat sensitive devices as the heat is only applied to the lead where the solder is present. It is also best suited for high density components. It is one of the few techniques that will solder components already attached to a heat sink and also heat pipes.
Shenzhen Vip Circuit Co., Ltd.(Vipcircuit) has listed Reflow Solder Equipment from the leading manufacturers. Click here to find reflow solder equipment.